Getting creative with cellulose
It is possible to extract plant-based fibres from crops, agricultural waste, household organic waste and old clothes. Researchers at Wageningen University & Research are developing technologies to reuse this cellulose, for example in coatings and varnishes, paper, construction materials and bioplastics. This will contribute to the circular economy and help sustainable and renewable alternatives to petroleum-based resources.
Cellulose is abundantly available in plant-based materials. “Cellulose is an essential component of wood fibres in trees, for example, and gives trees and plants their strength”, explains Christiaan Bolck, programme manager in renewable materials at Wageningen University & Research. Cellulose is also found in many waste products, such as household organic waste and waste flows from agriculture and food industries. However, much of this waste currently ends up in biodigesters and incinerators.
Substitute for plastics
Cellulose extracted from plants and waste flows can be used in all kinds of products, such as paper and cardboard, textiles, construction materials and coatings and varnishes. It can also be used to make plastics. “For example, materials made from cellulose can be used in packaging. This helps companies to respond to the increasing criticism of consumers regarding plastic packaging materials”, explains Bolck.
“Let’s not lose cellulose in waste flows when we can use it to make high-quality products.”
His colleagues have also developed a technology to turn flax fibres into biobased composites, which make plastic both stronger and lighter. “These can be used to make plastic mouldings, for example for the construction industry or in cars”, says Bolck.
Renewable resource
As well as making such great use of the cellulose in waste, there is another big advantage to developing new applications for the fibres. “Materials that we can make from cellulose can be used to replace materials used in industry that are currently made from petroleum. This means using sustainable, renewable resources rather than fossil-based resources”, explains Bolck. This applies not just to plastics, but also to coatings and varnishes. “For example, cellulose is used in high-gloss furniture varnishes.”
Technological know-how
“At Wageningen, we have a lot of knowledge when it comes to the different links in the value chain. First of all, we identify and analyse materials that contain high levels of cellulose, taking into account the quality of that cellulose. Next, we isolate the cellulose and modify it where necessary. The last step is implementation in the final application”, explains Bolck. Researchers at Wageningen have 35 years of experience in this process. Over time, they have come up with all kinds of applications for cellulose obtained from a wide range of crops and waste flows, or the other way round. “For some applications, for example, if you want to replace a petroleum-based material in a particular product, you need cellulose from a particular crop.”
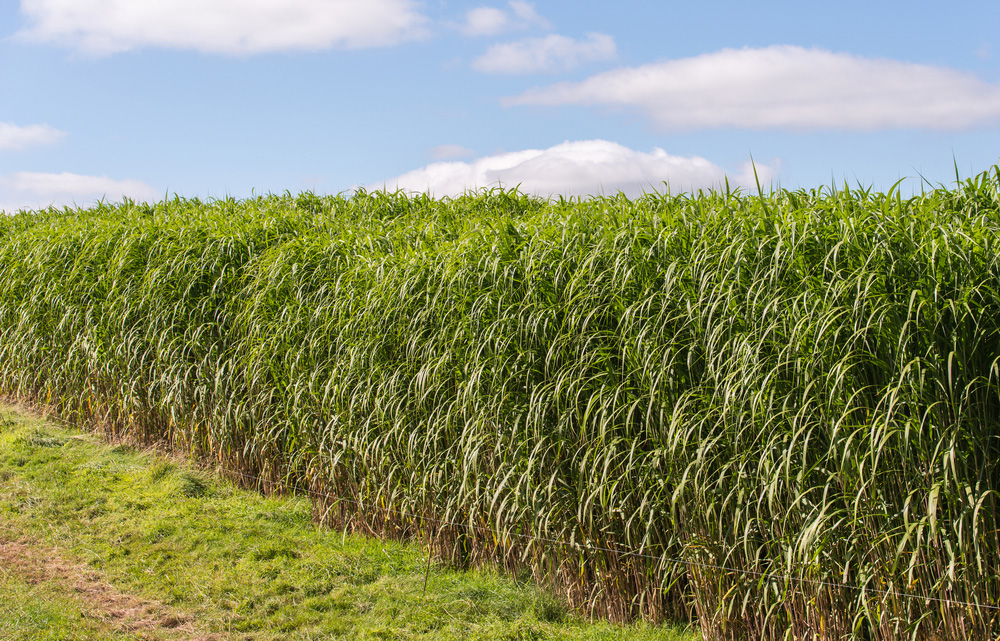
Elephant grass is a versatile, fast-growing crop from which cellulose can be extracted
Elephant grass and coconut husks
One versatile, fast-growing crop from which cellulose can be extracted is elephant grass. After processing, the fibres obtained from this crop can be used in biobased composites, paper and construction materials. Pulp left over from processing sugar beets also offers many possibilities as a source of cellulose.
Board materials for use in the construction industry can also be made from the fibres found in coconut husks. “We have developed a process in which coconut fibres are used to make board materials that are strong and water-resistant, with no need for other additives. In fact, we have rearranged the existing building blocks to make a product with much better properties than the original”, explains Bolck.
Textiles and tomato stems
Cellulose can also be extracted from other waste materials, such as the cotton in used clothing. However, a lot of cotton is not recycled because it contains elastane, which is why your old jeans can still end up in the furnace. “We have developed a process to separate the elastane, so that we can extract the valuable cellulose for use in other applications”, explains Bolck.
Just as exciting is the cardboard tomato packaging made from the leaves and stems of the very same tomato plants, which are currently sent to a biodigester or incinerator (see video above). Bolck: “To achieve this, we brought tomato growers in touch with a paper manufacturer, who were able to makes boxes from the leaves and stems of the tomato plants. It is not the most obvious connection.”
Urgent
The researchers at Wageningen apply not just their knowledge of materials and technology, but also of the chain from producer and processer to supplier and consumer. Through their extensive networks, they are able to link waste producers to potential consumers and help form new partnerships.
The urgency is increasing, believes Bolck. “The pressure to move away from a petroleum-based industry is increasing, as is the pressure to achieve a circular, biobased economy that makes optimum use of all material and waste streams.”
Read more:
- About unlimited possibilities for cellulose
- A brief introduction ‘What is bioplastic?’ and ‘Facts and fiction about bioplastics’
- Research into sustainable bioplastics
- Article on ‘Green chemicals’ and finding substitutes for petroleum-based products in cosmetics, detergents, paint and plastic
- Complete overview of bio-based building materials
- Background article ‘Towards a circular economy’
- Read this article in Dutch
Hola Christiaan.
Somos una empresa joven de fabricación de moda sostenible
de calzados, hemos leído algunos artículos tuyos y estaríamos encantados en colaborar en algún proyecto para sustituir el plástico en la producción de calzados.
Un saludo